Blowers/Fans
Centrifugal Blowers: Powering Industrial Air Movement
Centrifugal blowers stand as the backbone of industrial and commercial air movement, renowned for their efficiency, reliability, and adaptability across diverse applications. At the heart of these machines lies a simple yet robust design, meticulously engineered to deliver optimal performance in challenging environments.
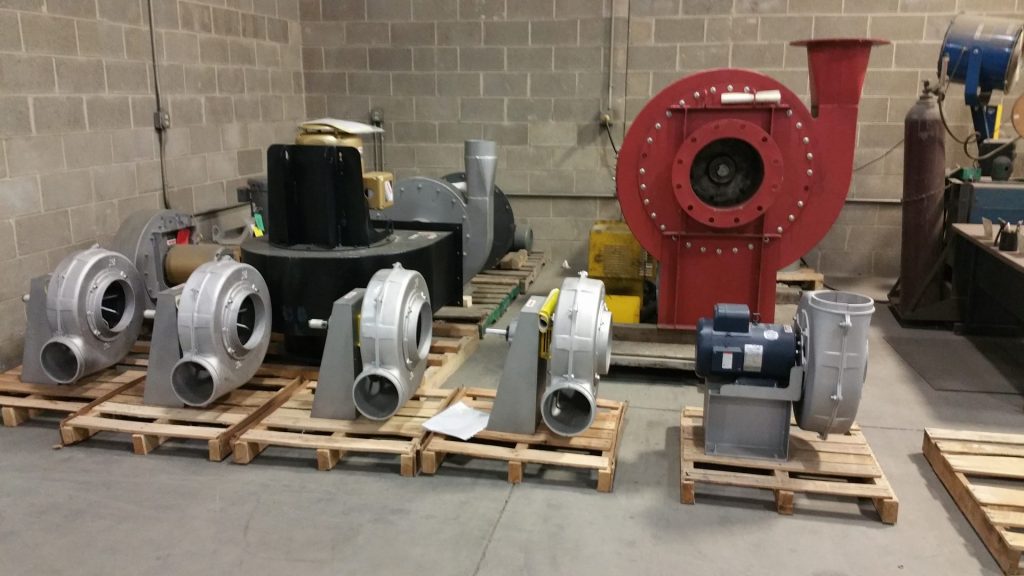
How Centrifugal Blowers Work
At their core, centrifugal blowers consist of a motor, a fan wheel, and a housing, working in harmony to generate powerful airflow. The electric motor drives the rotation of the fan wheel, which, in turn, propels air outward through the blower’s outlet. This ingenious design, coupled with a choice between direct or belt-driven mechanisms, allows for precise control over airflow speed and pressure.
The housing of a centrifugal blower plays a crucial role in directing airflow and safeguarding internal components from harsh industrial conditions. Constructed from durable materials like stainless steel or aluminum, the housing ensures longevity and resilience, even in the most demanding environments.
Unlike traditional fans, which push air parallel to the fan’s axis, centrifugal blowers draw air into the inlet, using the rotational force of the blades to expel it through the outlet. This unique airflow pattern enhances efficiency and effectiveness, making centrifugal blowers the preferred choice for various industrial processes.
Applications of Centrifugal Blowers
The versatility of centrifugal blowers extends across a wide spectrum of industrial applications:
- Clean Air Handling: From maintaining comfortable working conditions to removing harmful fumes, centrifugal blowers are instrumental in industrial air movement, offering configurations tailored to specific needs, such as backward curved or radial blades.
- Dust Loading: In dust collection systems, centrifugal blowers excel at capturing and moving particulate-laden air, improving air quality and safety in industrial environments.
- Pneumatic Material Handling: Centrifugal blowers play a vital role in transporting materials such as sand, pellets, and coal, ensuring constant pressure and efficient material flow in pneumatic systems.
- Saturated Air Handling: Specialized centrifugal blowers designed to handle saturated air conditions are essential for processes requiring humidity control, utilizing corrosion-resistant materials to withstand harsh environments.
- High-Temperature Applications: Engineered for durability and resilience, centrifugal blowers are indispensable in high-temperature environments such as industrial furnaces and ovens, ensuring reliable operation under extreme conditions.
- Dairy Processing: Centrifugal blowers uphold strict FDA regulations in dairy processing, facilitating air recirculation and drying processes while ensuring food safety standards are met.
- Incinerator Waste Disposal: From forced draft systems to fluidized bed furnaces, centrifugal blowers play a crucial role in waste disposal processes, ensuring efficient combustion and exhaust management.
Benefits of Centrifugal Blowers
The advantages of centrifugal blowers make them indispensable assets in industrial operations:
- Low Maintenance: With a simple yet robust design, centrifugal blowers require minimal maintenance, reducing downtime and repair costs.
- Energy Efficiency: High operational efficiency translates to reduced energy consumption, contributing to cost savings and environmental sustainability.
- Versatility: Centrifugal blowers adapt seamlessly to evolving industrial needs, offering flexibility and reliability across a wide range of applications.
- Durability: Engineered to withstand harsh industrial environments, centrifugal blowers offer exceptional durability and performance, ensuring reliable operation in demanding conditions.
In summary, centrifugal blowers represent the pinnacle of industrial air movement technology, combining efficiency, reliability, and adaptability to meet the diverse needs of modern industrial processes. From clean air handling to high-temperature applications, these versatile machines continue to drive innovation and progress across industries worldwide.
Industrial Fans: Enhancing Air Flow Efficiency
Industrial fans serve as highly efficient and robust devices designed to facilitate air flow in demanding environments. Constructed from durable materials such as cast aluminum and stainless steel, they are engineered to withstand rigorous conditions while ensuring consistent air circulation and pressure. Key components like ball or roller bearings, enclosed motor housing, and continuous welds contribute to their exceptional strength and longevity.
Types of Industrial Fans
Industrial fans come in various types, each tailored to specific air movement needs and environmental conditions. They can be broadly categorized into centrifugal and axial fans:
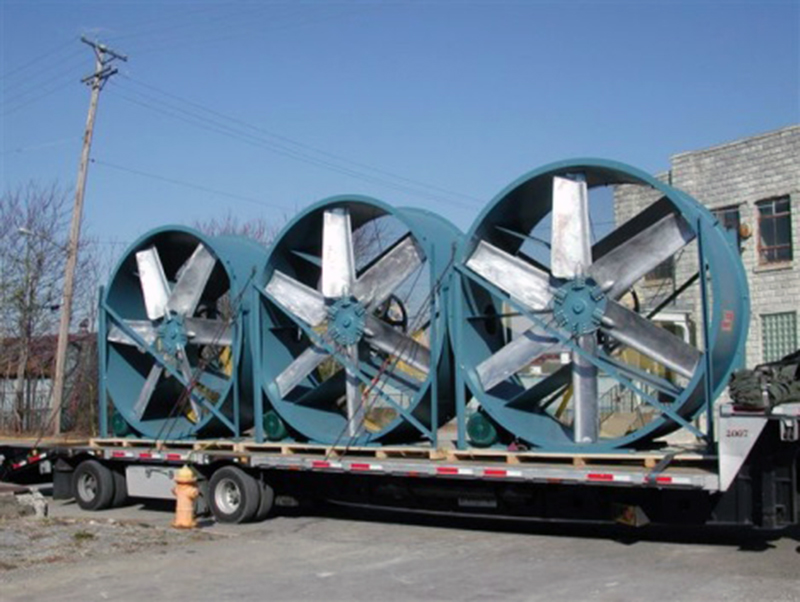
- Centrifugal Fans: Functioning akin to blowers, centrifugal fans pull air in using a rapidly rotating impeller and then discharge it at a 90° angle. They are suitable for applications requiring high pressure and volume.
- Axial Fans: Axial fans pull and push air parallel to their axis, facilitating axial outward transfer of air. Their design, determined by factors like blade configuration and casing, influences air flow volume and efficiency.
Within these categories, several subtypes exist, each with unique features and applications:
- Air Foil Fans: Equipped with flat standard blades, air foil fans are ideal for cooling towers, engine cooling, and refrigeration. They offer versatility with adjustable blade pitch angles for customized air flow.
- Backward Curved Fans: Featuring curved blades that prevent dust buildup, backward curved fans boast exceptional efficiency and are suited for high-pressure applications.
- Forward Curved Fans: Also known as squirrel cage fans, forward curved fans are commonly used in residential HVAC systems and low to medium static applications.
- Radial Blade Fans: Characterized by narrow, heavy blades extending radially from the hub, radial blade fans are suitable for high-pressure dust loading applications.
These are just a few examples among a diverse range of industrial fans tailored to specific industrial needs.
Applications of Industrial Fans
Industrial fans play a pivotal role across various industries, ensuring adequate air circulation and ventilation for worker safety and operational efficiency. From exhaust fans facilitating air removal in hazardous environments to cooling fans maintaining optimal temperatures in industrial settings, their applications are diverse and critical.
- Exhaust Industrial Fans: Designed for creating air flow and ventilation, exhaust fans find application in various settings, including commercial kitchens and industrial facilities.
- Duct Fans: In-line duct fans have small airflow capacity and are non fire rated. They are used where air flow is too low for a centrifugal fan and too high for a propeller fan. In-line duct fans have a flow rate of up to 2000 m3 per hour.
- Agriculture Industrial Fans: In agricultural settings, industrial fans help regulate temperature and humidity in livestock barns and greenhouses, promoting healthy breeding environments.
- Cement Industry: Fans used in cement manufacturing must withstand high temperatures and abrasion, playing crucial roles in processes like kiln induced draught and raw mill exhaust.
- Gymnasiums: Industrial fans for a gymnasium are wall mounted, which gives them greater flexibility and the ability to adapt to the gym layout. They are strategically placed to offer sufficient circulation to the available space. Most gyms have limited floor space since equipment or floors are used for physical activity.
- Chemical Industry: Operations in the chemical industry involve the handling and use of hazardous and flammable substances and materials that require proper and safe storage.
- Power Generations Industry: The power generation industry uses forced draft, induced draft, and dust control fans that are required to operate at extremely high temperatures.
- Pneumatic Conveying: Industrial fans are used in conveying systems to move cereal, grains, wood chips, and powdered materials. The process of pneumatic conveying is used by the food, mineral, plastics, coffee, and pharmaceutical industries.
- Automotive Industry: Industrial fans in the automotive sector ensure worker safety by operating reliably in hazardous environments.
- Oil and Gas Industry: Industrial fans in oil and gas operations are engineered to withstand harsh conditions, including extreme temperatures and corrosive atmospheres.
These examples underscore the indispensable role of industrial fans across diverse sectors, contributing to operational efficiency and worker safety.
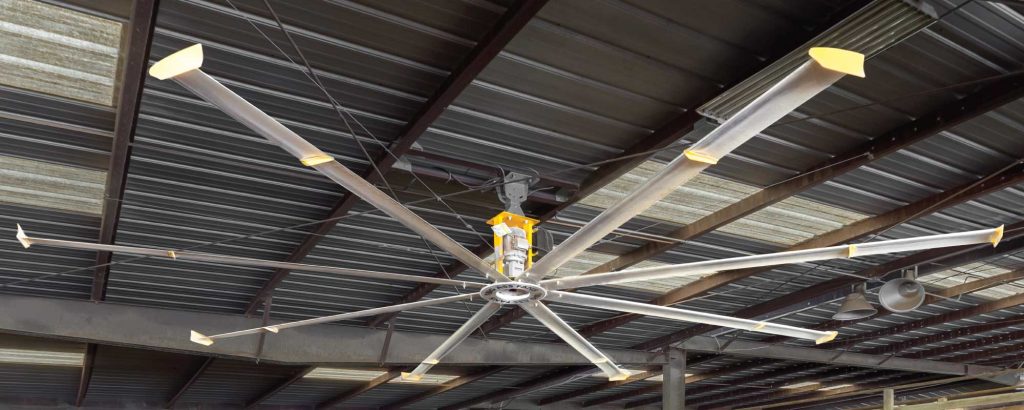
The Air Movement and Control Association (AMCA)
Established in 1955 through the amalgamation of several industry associations, the AMCA is dedicated to developing standardized methods for certifying and classifying heating, ventilation, and air conditioning equipment. Through voluntary membership and adherence to established standards, the AMCA ensures the quality and reliability of industrial fans.
AMCA certifications guarantee compliance with industry standards, providing assurance of fan performance and safety. The association’s Spark Resistant Construction (SRC) standards, categorized into Types A, B, and C, further ensure fan safety in hazardous environments.
In summary, industrial fans represent a vital component of various industries, providing essential air flow solutions for diverse applications. From maintaining optimal conditions in industrial processes to ensuring worker safety in hazardous environments, these fans play a pivotal role in operational efficiency and workplace well-being. Supported by organizations like the AMCA, industrial fans continue to evolve, meeting the ever-changing demands of modern industries.